Continuous Improvement Projects
Based on our principal consultant's Continuous Improvement (CI) work before launching CI DESIGN CONSULTING LLC in December 2024.
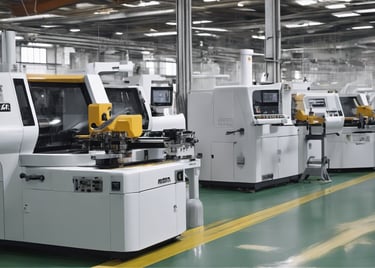
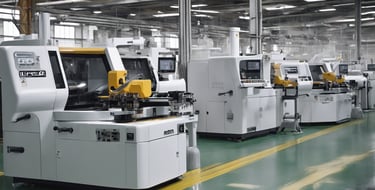
1 | Product CI
Improve quality, reliability, gross margins, safety, and compliance.
Product CI - Cost Reduction
The product cost for large industrial equipment was too high, $1M+.
Methodical material cost analysis, the Pareto principle, value engineering methods, and commercial negotiations reduced product cost by 15%.
Product CI - Serviceability Improvement
Product serviceability for an analytical instrument was unacceptable: replacing a turbo pump took 2+ hours.
Revised the design to reduce turbo pump replacement effort to 20 minutes.
Product CI - Noise Reduction
Acoustic noise emissions of an analytical instrument were excessive. Customers threatened to return machines. Two engineering teams attempted to address the issue without success.
Analyzed the noise mechanisms, then designed and implemented a noise reduction kit on 500+ machines at customer sites. One customer noted: "Now it's too quiet! We need a status light to know the machines are running."
Product CI - Cycle Time & Cost Reduction
The complex triple-stage vacuum and RF system for an analytical instrument included multiple separate chambers.
Combined the functions of all chambers into a single aluminum casting for improved precision, reduced assembly effort, and 30%+ cost reduction.
Product CI - Reliability Improvement
DC power supplies for industrial machines had an unacceptable failure rate, causing machines to stop at the customer's factories.
Analyzed the failure mechanisms, identified the root causes, and implemented solutions to reduce the failure rate by 50%+.
2 | Process CI
Improve supply chains, lean manufacturing, efficiency, cost-effectiveness, quality, and resilience.
Process CI - Manufacturing Efficiency
Assembly cycle time and effort for industrial machines were too high, with 500+ work hours.
Methodical workflow analysis guided the design of optimized and lean workflows to reduce product assembly effort by 50%.
Process CI - Production Test Efficiency
Product test cycle time and test effort for industrial machines were too high, with 600+ work hours.
Methodical analysis guided workflow improvements, design changes, and test automation to reduce product test effort by 60%.
Process CI - Quality Improvement
Engineers encountered too many quality issues during industrial machine installations at the customer sites.
Designed and implemented an installation defect scoring method and methodically addressed root causes to reduce defect scores by 50%+.
Process CI - Production Resilience
Ongoing obsolescence issues plagued equipment production flow, causing manufacturing floor escalations and ship schedule risks.
Designed and implemented a proactive obsolescence risk forecasting process with 200+ suppliers. Implemented digital workflows with risk data in the product design process and production to improve obsolescence resilience by 20%+.
Process CI - Configuration Management
The product structure for sizeable industrial equipment was not designed to meet customers' unique requirements, resulting in high rework costs and ship delays.
Designed and implemented a highly configurable product structure to enable 20%+ efficiency improvements and allow product reconfigurations late in the production cycle to respond to requirement changes.
Process CI - Change Management
The product Engineering Change Order (ECO) process cycle time was excessive, causing supply chain and production issues.
Designed and implemented a structured ECO process that reduced cycle time by 3x, from several weeks to just a few days.
Process CI - Supply Chain Scalability
Supply chain scalability and resilience had to be assessed for a startup with 30+ suppliers.
Implemented a supplier assessment framework with about ten criteria and scored 90% of suppliers to identify strengths, gaps, and risks.
3 | Operations, Program & Compliance Mgt.
Assess and improve business processes.
Ensure effective project execution.
Ensure products & work areas comply with safety, EHS, and ISO standards.
Operations Management
After a recent downsizing, an equipment company realized a drastic increase in unexpected orders for multi-million dollar machines.
Scaled the supply chain, and ramped production capacity by 4x with 24/7 operation within a few months.
Program Management
A large US equipment company had acquired a small German startup. The teams had to be integrated to develop a joint product based on the startup's manual prototype.
Led the program with 20+ engineers to transfer the technology and integrate the teams to develop an automated, production-worthy metrology tool.
© 2025. All rights reserved.
CI DESIGN CONSULTING LLC
torsten@cidesignconsulting.com